Predictive Maintenance: The Secret to Reliable Operations
- Aritrya Sen
- Sep 3, 2024
- 9 min read
Unplanned downtime is a costly burden, with the median cost across 11 industries hovering around $125,000 per hour. In sectors like oil and gas, chemicals, and metals, where critical unplanned outages can occur multiple times a year, the financial impact is even more staggering. The challenge lies in preventing these costly disruptions. Investing in predictive maintenance offers a solution, with the potential to pay for itself with just one accurate prediction, saving companies from the significant losses associated with unplanned downtime.
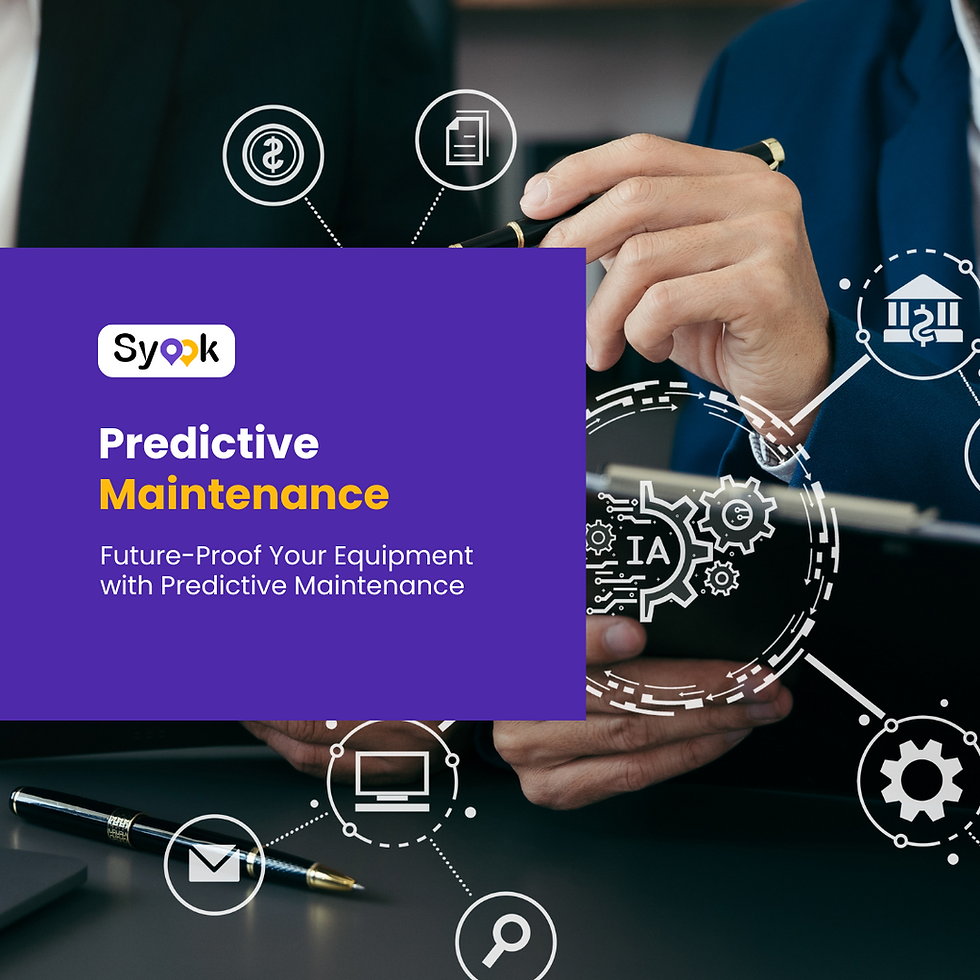
In today’s fast-paced industrial world, maintaining equipment reliability is critical. Unexpected downtime can result in lost productivity, costly repairs, and even safety risks. This is where predictive maintenance (PdM) technologies, a key component of Industry 4.0, come into play. But what exactly is predictive maintenance, and why is it considered a game-changer?
Here’s a summary of the article in short bullet points:
Unplanned downtime costs industries around $125,000 per hour, particularly impacting sectors like oil and gas, chemicals, and metals.
Predictive maintenance (PdM) can significantly reduce these costs by predicting equipment failures before they occur.
Evolution of maintenance from reactive (Maintenance 1.0) to preventive (2.0), condition-based (3.0), and predictive (4.0) approaches.
Maintenance 4.0 leverages IoT, AI, and big data for predictive insights.
PdM uses real-time data from IoT sensors and machine learning to predict failures.
Key benefits include reduced downtime, cost savings, extended equipment lifespan, enhanced safety, and sustainability.
Indirect Failure Prediction: Uses machine health scores, scalable but less precise.
Anomaly Detection: Identifies deviations from normal behavior, lower data requirements, potential for false positives.
Remaining Useful Life (RUL) Estimation: Predicts exact time before failure, highly precise but resource-intensive.
High startup costs, complexity in integration, data quality requirements, and risk of over-reliance on technology.
Widely used in manufacturing, energy, transportation, oil and gas, and telecommunications for improving reliability and efficiency.
Growth of IoT and big data, rise of digital twins, emergence of Predictive Maintenance as a Service (PMaaS), and integration with CMMS/EAM platforms.
Predictive maintenance is a proactive strategy that offers significant benefits, making it essential for future industry competitiveness.
Let’s explore how PdM works, its benefits, and its role in transforming industries through IoT, condition monitoring, and predictive analytics.
The Journey to Predictive Maintenance
The concept of maintenance has undergone a significant evolution over the past century, transforming from simple reactive approaches to highly sophisticated predictive systems. This evolution is often categorized into four phases: Maintenance 1.0 to Maintenance 4.0.
Maintenance 1.0 represents the earliest form of maintenance, where the primary approach was reactive. Equipment was fixed only after it broke down, leading to significant downtime and high costs. There was no foresight, and the unpredictability of failures was a constant challenge.
As industries began to understand the importance of minimizing downtime, Maintenance 2.0 emerged. This phase introduced preventive maintenance, where routine checks and scheduled maintenance were performed to prevent equipment failures. While this approach reduced the occurrence of breakdowns, it was still inefficient as it often led to unnecessary maintenance activities.
The advent of computers and the Internet brought us to Maintenance 3.0. This phase saw the introduction of condition-based maintenance (CBM), where maintenance decisions were based on the actual condition of equipment rather than on a fixed schedule.
This approach was more efficient, as it relied on sensor data to monitor equipment health. However, it still lacked the predictive capabilities to anticipate future failures accurately.
Today, we stand at the threshold of Maintenance 4.0, driven by the integration of IoT, AI, and big data analytics. This phase, also known as predictive maintenance, leverages advanced technologies to predict when and how equipment might fail, allowing for timely interventions that minimize downtime and optimize resources.
The Rise of Predictive Maintenance
What is Predictive Maintenance? Predictive maintenance (PdM) represents the pinnacle of maintenance strategies, combining the best aspects of its predecessors while introducing new levels of efficiency and foresight. By analyzing data collected from equipment sensors and using advanced algorithms, predictive maintenance can forecast potential failures before they happen. This approach not only reduces unplanned downtime but also extends the lifespan of machinery and equipment.
Predictive maintenance is a data-driven approach that leverages advanced technologies like IoT (Internet of Things), condition-based monitoring (CBM), and machine learning (ML) to predict equipment failures before they occur. Instead of adhering to a rigid maintenance schedule, PdM solutions analyze real-time data from various sensors to determine the optimal time for maintenance activities.
For instance, sensors can monitor critical parameters like vibration, temperature, and lubrication quality. This data is processed using predictive maintenance analytics to detect patterns and anomalies that signal potential issues. This proactive approach allows businesses to schedule maintenance only when necessary, reducing unnecessary downtime and extending the lifespan of machinery.
How Does Predictive Maintenance Work?
Predictive maintenance relies on a combination of IoT, data analytics, and specialized maintenance software to keep equipment in peak condition. Here’s
a breakdown of the process:
Data Collection: IoT-enabled sensors continuously collect data from equipment. This can include vibration analysis, motor current analysis, and other condition-monitoring techniques.
Data Analysis: The collected data is fed into a predictive maintenance system, where AI and machine learning algorithms analyze it to identify patterns. This step is crucial in condition-based monitoring, as it enables the detection of early warning signs of equipment failure.
Prediction and Alert: When the system identifies a potential issue—such as abnormal vibration indicating misalignment—it generates an alert. This alert is sent to the maintenance team, who can perform the necessary tasks before a breakdown occurs.
Continuous Improvement: As more data is collected, the predictive maintenance program becomes increasingly accurate, refining its predictions and improving decision-making over time.
Predictive Maintenance vs. Prescriptive Maintenance
It’s important to distinguish between predictive maintenance and prescriptive maintenance. While PdM focuses on predicting equipment failures, prescriptive maintenance goes a step further by recommending specific actions to prevent those failures.
Prescriptive maintenance uses advanced analytics to not only predict when equipment will fail but also suggest the best course of action to mitigate the risk. This could include adjusting operational parameters, scheduling maintenance, or replacing components.
The Benefits of Predictive Maintenance
Predictive maintenance offers several advantages over traditional maintenance strategies like preventive maintenance. Here’s how it makes a significant impact across various industries:
Reduced Downtime: By predicting and preventing failures, PdM minimizes unplanned downtime, ensuring continuous operations and maximizing productivity.
Cost Savings: Predictive maintenance helps avoid unnecessary maintenance tasks and reduces the need for spare parts. Addressing issues early also prevents more extensive and expensive repairs.
Extended Equipment Lifespan: Regular monitoring through predictive maintenance ensures that equipment remains in optimal condition, extending its useful life and improving return on investment.
Enhanced Safety: By identifying potential issues before they become critical, PdM reduces the risk of accidents and creates a safer working environment.
Sustainability: Predictive maintenance contributes to sustainability by optimizing energy use and reducing waste, thereby minimizing the environmental impact of industrial operations.
Types of predictive maintenance
As the predictive maintenance landscape has evolved, three key types have emerged, each with its unique strengths and challenges: Indirect Failure Prediction, Anomaly Detection, and Remaining Useful Life (RUL) estimation.
While they share a common goal—keeping machines running smoothly—their approaches, data analysis methods, and the insights they provide set them apart. Let’s dive into what makes each of these types stand out and how they fit into the modern maintenance toolkit.
1. Indirect Failure Prediction: The Reliable Workhorse
Indirect failure prediction is like the steady, dependable workhorse of predictive maintenance. It’s been around the longest and is still widely used today. This approach typically assigns a “machine health score,” which is a blend of factors like maintenance history, operating conditions, and how long the equipment has been in use. While this method often uses general analysis to arrive at this score, it can also leverage supervised machine learning if there's enough data available.
Why It’s Popular:
Scalability: Indirect failure prediction scales well, mainly because it leans on manufacturers’ specifications that are fairly standard across similar machines. This makes it easier to apply to a broad range of equipment without a lot of customization.
Cost-Effective: Since it often uses existing sensors and data, there’s no need for additional pricey equipment or complex setups.
But There Are Trade-Offs:
Time-Window Accuracy: One of the main drawbacks is that it doesn’t provide a precise timeline for when a machine might fail. For industries where downtime is expensive—like those with heavy machinery—this can be a significant limitation.
Dependency on Historical Data: Its effectiveness hinges on having a rich history of data to model from. Without it, predictions can be less accurate.
2. Anomaly Detection: The Rising Star
Anomaly detection is the new kid on the block, gaining popularity as it brings a fresh approach to predictive maintenance. Unlike indirect failure prediction or RUL estimation, which focus on past failures to predict future ones, anomaly detection zeroes in on what’s “normal” for a machine. It then flags anything that deviates from this normal behavior as a potential issue, whether it’s a fault, defect, or early sign of failure.
Why It’s Gaining Ground:
Lower Data and Hardware Needs: You don’t need a ton of data or high-end computing power to make anomaly detection work. This makes it accessible and cost-effective, even for smaller operations.
Highly Scalable and Transferable: Because these models learn what’s normal, they can be easily applied to different machines without needing a lot of retraining, making them versatile across various environments.
But There’s a Catch:
Time-Window Accuracy: Like indirect failure prediction, anomaly detection doesn’t tell you exactly when a machine will fail. This uncertainty can be problematic in industries where precise timing is crucial.
False Positives: While many solutions can distinguish between critical and non-critical issues, the choice of machine learning model is essential. If the model isn’t sophisticated enough, you might end up with too many false alarms, which can be frustrating and inefficient.
3. Remaining Useful Life (RUL): The Gold Standard
RUL estimation is often seen as the gold standard in predictive maintenance. It’s all about predicting how much life a machine has left before it needs repair or replacement, measured in terms of cycles, hours, or any other relevant metric. RUL relies on condition indicators extracted from sensor data, tracking the gradual degradation of a system to predict when it will reach the end of its useful life.
Why It’s So Powerful:
Precise Time-Window for Failure: RUL is particularly valuable in industries where maintenance costs are sky-high, and advanced planning is essential. Knowing exactly when a machine is likely to fail allows for optimal scheduling of maintenance activities, minimizing downtime and costs.
Robust Output: Because RUL estimates are based on high-quality, detailed data, they tend to be reliable and provide a strong foundation for decision-making.
But It’s Not Without Challenges:
High Resource Demand: Training the complex models needed for RUL estimation requires significant computing power, especially if done in-house. This can make it less accessible for smaller companies.
Limited Scalability: Different environments and usage patterns can lead to varying failure modes for the same equipment. This means that RUL models often need to be retrained for each specific scenario, which limits their scalability and generalizability.
Industry Applications of Predictive Maintenance
Predictive maintenance is being widely adopted across various industries, enhancing reliability and efficiency. Here are some key applications:
Manufacturing: In the manufacturing sector, predictive maintenance helps avoid disruptions to production lines, reducing downtime and improving overall efficiency. PdM technologies such as vibration analysis are commonly used for monitoring machinery health.
Energy: Power generation and distribution companies use predictive maintenance to prevent outages and ensure the continuous supply of energy. PdM is especially critical in maintaining the health of turbines, transformers, and other essential equipment.
Transportation and Fleet Management: Predictive maintenance is crucial in the transportation industry, including fleet management. By monitoring the condition of vehicles, PdM ensures timely maintenance, reducing the risk of breakdowns and improving safety.
Oil and Gas: In the oil and gas industry, predictive maintenance is vital for managing the health of critical infrastructure. PdM helps detect potential issues in pipelines, pumps, and other equipment, preventing costly disruptions.
Telecommunications: Network reliability is essential in telecommunications. Predictive maintenance helps monitor and maintain the health of network infrastructure, reducing the risk of service interruptions.
The Future of Predictive Maintenance
The future of predictive maintenance looks promising as technologies like IoT, AI, and machine learning continue to advance. Here are some trends to watch:
IoT and Big Data: The growing use of IoT in predictive maintenance is generating vast amounts of data, enhancing the accuracy and effectiveness of PdM systems. IoT-based predictive maintenance allows for real-time monitoring and more precise predictions.
Digital Twins: Digital twins—virtual replicas of physical assets—are becoming increasingly important in predictive maintenance. They enable businesses to simulate real-world conditions and predict outcomes without risking actual equipment.
Predictive Maintenance as a Service: As PdM technologies become more accessible, we’re likely to see the rise of predictive maintenance as a service (PMaaS). This model allows companies to leverage predictive maintenance solutions without significant upfront investments.
Integration with CMMS and EAM: Integrating predictive maintenance with computerized maintenance management systems (CMMS) and enterprise asset management (EAM) platforms will streamline maintenance processes and improve decision-making.
Predictive maintenance represents a significant shift in how businesses manage equipment health. By leveraging IoT, condition monitoring, and advanced analytics, PdM offers a proactive, cost-effective approach to maintenance. While there are challenges to implementing predictive maintenance solutions, the benefits—reduced downtime, cost savings, extended equipment lifespan, and enhanced safety—make it a compelling strategy for the future.
As Industry 4.0 technologies continue to evolve, predictive maintenance will become increasingly essential in maintaining a competitive edge across industries. Maximize your enterprise assets' potential with Syook’s connected assets and CMMS. Our unified platform integrates maintenance, inspection, and reliability systems into a single, cloud-based solution. Leveraging AI, IoT, and advanced analytics, it optimizes asset performance, extends lifecycles, reduces operational costs, and minimizes downtime.
Comments