RTLS + Sensors: Oil & Gas Industry
- Team Syook
- Nov 14, 2022
- 2 min read
Updated: May 30, 2024

“The liquid gold” is what we call petroleum. Rightly so, it has been on the news and on our minds for the past few months. The fluctuating prices of oil are the talk of the town. So why not make it the theme of our discussion? Oil is a precious commodity not only because it is limited in availability but also because of the cumbersome extraction process. The oil and gas industry operates in harsh conditions with high regard for cost and safety. These operations have to be-
Process-oriented
Cost-effective
Safely complaint
But what is missing here?
With growing prices, market competition, and new EV technology coming out, it's very critical to be efficient in operations and ensure maximum safety and maximum asset utilization.
The oil & gas industry still struggles with some key challenges contributing to COI (cost of inaction) like –
Inconsistent inventory
Cost of unused equipment
Asset losses
Safety of workers & assets
How do RTLS and sensors solve this problem?
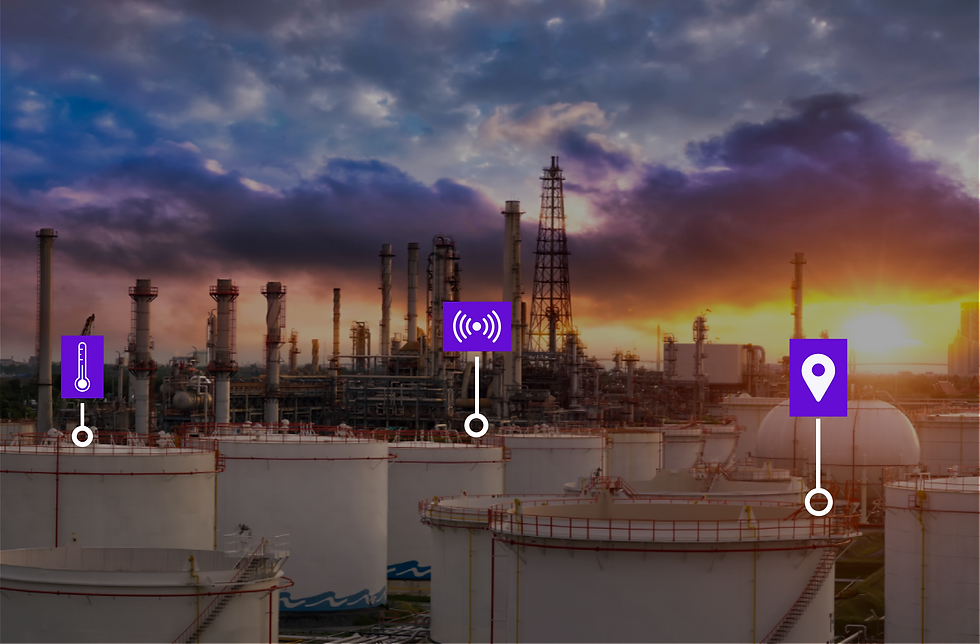
RTLS system helps track the location of personnel and assets on the floating platforms, drilling rigs, refineries, tools & equipment warehouses, and much more. Also, critical data can be gathered using sensors, e.g.,
-> Temperature monitoring of LNG pipelines
-> H2S gas leak detection in refineries
-> Personnel vitals monitoring, etc.
An ecosystem can be built to replicate the plant. This idea of replication is now being called “the digital twin”. A virtual copy of the plant will help in capturing and mapping essential information data.
How exactly is it going to help the oil and gas industry –
-> Digital twins or smart eco-systems powered by RTLS & sensors can help oil and gas operators save up to 15% on total project costs. -> It is estimated that approximately 74% of organizations will adopt a digital twin by 2025.

Safety in Oil & Gas
One key challenge that the Oil and Gas industry continues to face is creating a safe environment for its operations. An article published by The Washington Post talks about the underreporting of methane leaks. This occurs due to a lack of –
Surveillance that can be enabled through automation
Continuous tracking and monitoring of surroundings
Digitization in the processes
To reduce the impact of NOx or SO2 (by-products), tracker controllers are non-negotiables. Sensors are effective in detecting emissions and can alert in case of breaches. These mishaps can be mitigated by deploying a cohesive and robust RTLS system.
Safety is only one of many concerns in the Oil and Gas industry, RTLS and sensors can resolve many such challenges…
How can RTLS bring down costs?
Let’s take an example, some of the equipment used for drilling (rotary tools, casing tools, etc.) are often rented from contractors. These rental provisions are expensive, the cost is in the range of $2000 to $5000 per day. If this equipment goes unused, there is a significant loss incurred due to a lack of efficient management.
This can be solved by linking attributes of partially reusable equipment and capturing data for the additional parameters defined by the rig. E.g.,
“Drill bit has been used only for 200ft, can be still used for 800ft.”
Workflows like these are easy to configure and track in RTLS-driven platforms. This segregation helps operators save millions of dollars.
Comentarios